Автор: Антон
На сегодняшний день радиолюбители используют 2 основных способа изготовления печатных плат: ЛУТ (лазерно – утюжная технология) и фотолитографию – использование различных видов фоторезиста. Остальные работают по-старинке: лак, маркер, скотч и т.д. – оставим это для мазохистов. Во всех случаях встает вопрос защиты дорожек от окисления, коротких замыканий и прочих напастей.
В качестве решения зачастую любителями используется лужение проводников, из чего вытекают следующие недостатки: кустарный вид полученной платы, иногда – перегрев и отслаивание печатных проводников при лужении, опасность образования тонких перемычек из припоя, повышенная ёмкость между соседними дорожками. Решение всех вышеозначенных проблем – паяльная маска.
После изучения информации о промышленных способах ее нанесения, как современных – жидкие паяльные маски, так и ушедших в прошлое – плёночных масках, возникла идея нанесения маски в домашних условиях с помощью фоторезиста.
После N-го количества различных неудачных попыток, ошибок – я пришел к стабильному качественному результату. Рассмотрим технологию на наиболее сложном примере – двусторонней печатной плате.
Технология довольно трудоёмка и занимает приличное количество времени, особенно при отсутствии опыта, но результат с лихвой окупает эти затраты.
Для процесса понадобятся:
1) Плёночный фоторезист (желательно от нижегородского завода «Репер», у него самое высокое разрешение, низкая цена и проверенные свойства – я использовал ф/р марки «ПНФ-ВЩ»);
2) Ламинатор, пусть даже самый недорогой. В крайнем случае – просто утюг;
3) Лазерный или струйный принтер для печати фотошаблонов;
4) Ультрафиолетовая лампа с длиной волны примерно 365 нм (с чёрной колбой). Дело в том, что на 365 нм приходится пик чувствительности указанного фоторезиста;
5) Кальцинированная сода – проявитель фоторезиста, продается за копейки в любом хозяйственном магазине;
6) Обычный этиловый спирт, для снятия засвеченного фоторезиста;
7) Пакетики с замками, достаточного размера, чтобы разместить в них плату;
8) Листы стекла, о размерах которых будет рассказано ниже;
9) Металлическая линейка или штангенциркуль;
10) Канцелярский нож, чем острее – тем лучше;
11) Булавки – 4 шт;
12) Металлические канцелярские зажимы, позволяющие зажать предметы толщиной до 1 см.
Процесс изготовления начинается с печати фотошаблонов, причём одну из сторон надо печатать зеркально, для того, чтобы к обеим сторонам платы шаблоны прилегали чернилами – так получается более чёткий рисунок. Для начала лучше потренироваться на обычной бумаге.
Плёнки бывают разные, есть универсальные, а есть рассчитанные только на один вид печати – лазерную или струйную. Больше всего мне понравились плёнки «Folex», у их «струйных» и «универсальных» пленок очень мелкое зерно, малые деформации при лазерной печати. Плёнка для струйной печати «Lomond» оставила плохое впечатление: крупное зерно и как следствие – низкая чёткость краёв.
Внимание! Вышеуказанный фоторезист негативный, то есть затвердевают и не смываются засвеченные участки, следовательно при печати шаблона надо сделать его негатив! (Дорожки должны быть прозрачными).
При печати на лазерном принтере происходит деформация пленки, обусловленная температурными воздействиями и ошибками линейной развёртки, потому зачастую необходимо делать калибровку – для начала нарисовать и вывести на печать обычную линейку, затем штангенциркулем или металлической линейкой измерить ее фактическую длину, внести соответствующие поправки на деформацию. Программы SprintLayout и DipTrace, начиная с версии 2.1. (Ветка по DipTrace, Ветка по Sprint layout) поддерживают данную опцию. В любом случае, лучше проверить свой принтер на предмет искажения размеров. К тому же при использовании лазерной печати возможно понадобится оптическое уплотнение тонера специальным спреем «Density Toner», говорят, что еще помогает держание шаблона над парами ацетона.
У меня струйный принтер «Epson R270», чернила неоригинальные – «InkTec», тут столкнулся с весьма тяжёлыми граблями – у этих «водяных» чернил оказалась маслянистая основа, в результате чего некоторая часть чернил, которая почему-либо осталась не закреплена покрытием плёнки, не высыхает до конца и при касании чего-либо, это "что-либо" пачкает. При повторной протяжке загрязняет механизмы принтера и те в свою очередь оставляют следы на ненапечатанной части плёнки (До этого был «Epson R220» с чернилами «Profiline» – подобные проблемы отсутствовали). Решение было найдено – сначала подсушить шаблон феном в течении нескольких минут, затем посыпать мелким порошком, у меня прижилась для этой цели финишная шпаклёвка «Vetonit». Можно попробовать детскую присыпку. Порошок нужно легко втереть пальцем в рисунок, затем лишнее стряхнуть, затем удалить лишнее мягкой тряпочкой. После этого шаблон готов к дальнейшим действиям.
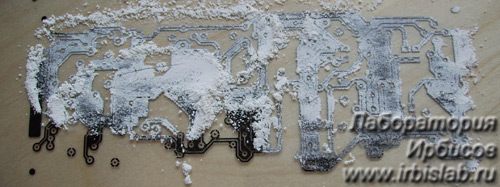
Рисунок 1 – Закрепление чернил
Следующий этап – совмещение и скрепление фотошаблонов. Для этого необходима ровная и не очень жёсткая поверхность: картон или десяток листов бумаги.
Фотошаблоны совмещаются в соответствии с рисунком 2 – напечатанными сторонами вовнутрь, друг к другу. Затем, как можно точнее к перпендикулярному к плоскости положению прокалываются 4-мя булавками.
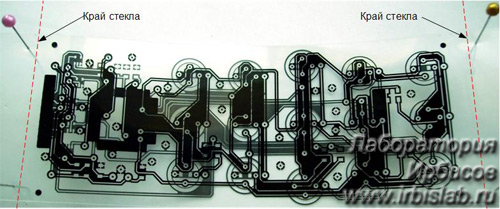
Рисунок 2 – Совмещение фотошаблонов
Это позволит в дальнейшем точно совместить стороны при помещении между шаблонами заготовки платы и не допустить смещения относительно друг друга осей сквозных выводов.
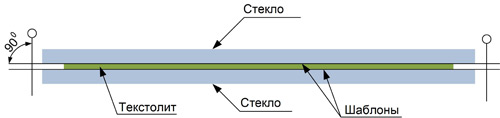
Рисунок 3 – Схема совмещения сторон фотошаблонов
Как видно из рисунков 2 и 3 – необходимы два стекла, накрывающие с запасом в несколько миллиметров заготовку, но уже, чем расстояния между булавками, чтобы можно было корректировать положение шаблонов относительно друг друга. Толщина стёкол должна быть не менее 2,5 мм, иначе возможны прогибы и неплотное прилегание фотошаблонов. Пленка в местах проколов при сборке всего в единое целое, должна быть раздвинута на толщину, равную или немного большую, чем толщина заготовки.
Таких обрезков стекла я набрал целую коробку бесплатно в ближайшей стекольной мастерской, отдали с удовольствием. Так же нужно иметь стеклорез для точной подгонки размеров.
ВАЖНО! Техника безопасности: Работайте в очках, в перчатках или толстой тряпкой, не поленитесь затупить края стекол мелкой шкуркой под струей воды, так потом не порежетесь и не надышитесь вредной стеклянной пылью.
Всё! Теперь нужно подготовить текстолит, самый ответственный этап – обезжиривание, здесь очередные грабли не меньшего калибра: по идее, это можно сделать бензином/спиртом/ацетоном, но мне так и не удалось достать ничего из перечисленного без «левых» примесей – всегда оставались следы после обработки, и фоторезист никак не хотел прилипать так, как должен. Помогло следующее – моем руки со стиральным порошком (лучший эффект дал «Tide»), дабы обезжирить, берём мелкую шкурку, смачиваем водой её и заготовку, посыпаем мокрый текстолит тем же порошком и зачищаем (без фанатизма – медь не продерите) до блеска, смываем под струей горячей воды (хоть руки и вымыты, всё равно касаться подготовленной меди нельзя – держим заготовку за края). По окончании процесса заготовка протирается насухо, предварительно выстиранной х/б тряпкой. К поверхности, подготовленной таким образом, фоторезист приклеивается так, как нужно.
Затем нужно заламинировать заготовку платы фоторезистом, в моём случае он покрыт с разных сторон двумя плёнками – лавсановой (гладкой и блестящей) с одной стороны, и полиэтиленовой матовой с другой. Согласно инструкции производителя нужно снять полиэтиленовую плёнку, лавсановую оставить – она служит для защиты от кислорода воздуха, без неё фоторезист не будет полимеризоваться. Кусок фоторезиста вырезается с запасом, чтобы перекрыть заготовку с каждой стороны минимум на 2 см. Затем текстолит кладется на лист бумаги, накрывается фоторезистом и отправляется в ламинатор. Как только ламинатор захватит текстолит – свободный край фоторезиста надо слегка приподнять, при этом избегать натяжения, иначе возможны складки и перекосы. Это необходимо для исключения образования пузырьков воздуха, ну и разумеется, перед тем, как сунуть в ламинатор – убедиться в отсутствии пыли на поверхности заготовки.
В том случае, если каким-то образом Вы все же умудрились сделать пузырёк воздуха, то его можно попробовать проколоть иголкой, и снова пропустить через ламинатор.
После первого прохода необходимо канцелярским ножом обрезать лишний фоторезист по краям заготовки, причём надо кончиком ножа проколоть плёнку в середине, и двигаться к углам платы – так защитная пленка не будет сдираться. После обрезки аналогично заламинировать вторую сторону.
Как только обе стороны заламинированы, нужно все это пропустить через ламинатор еще пару-тройку раз, чтобы хорошо прогреть текстолит и намертво прикатать фоторезист. В случае же с утюгом – результат гораздо сильнее зависит от степени кривизны лап, но нет ничего невозможного
. Главное – не перегреть, температура не должна превышать 150 °С.
Теперь можно и экспонировать. Собираем весь бутерброд, как показано на рисунке 2, выравниваем булавками положение фотошаблонов, зажимаем всё это между стеклами и скрепляем зажимами, в качестве которых отлично подойдут металлические канцелярские, которых у меня, к сожалению, на тот момент не было, потому воспользовался прищепками.
Главное, чтобы эта вся конструкция была надежна, стекла не смещались, иначе придётся все переделывать заново, начиная с этапа подготовки текстолита. Я применил 8W УФ-лампу «Vito». При расстоянии от лампы до платы 15 см требуемое время экспонирования фоторезиста около 2 мин.
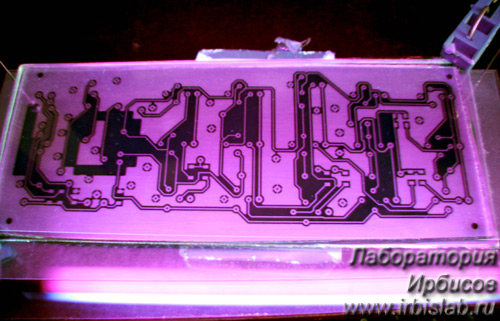
Рисунок 4 – Процесс экспонирования
Если экспонирование прошло удачно, то сразу же разбираем бутерброд, удаляем защитную плёнку – так наша заготовка перестанет бояться света. Можно проявлять, для этого необходимо заранее приготовить (1–2) % раствор кальцинированной соды ((10–20) г на 1 л воды), температура значения не имеет.
Для ускорения процесса проявки – так меньше вероятность повредить тонкие проводники, мною была использована косметическая губка (в сухом состоянии она жёсткая, но при размачивании становится очень мягкой), подобная той, которая изображена на рисунке 5 – она эффективно смывает фоторезист и не повреждает дорожки. При проявке необходимо уделить особое внимание тонким зазорам и отверстиям в контактных площадках. Не делайте зазоры уже 0,25 мм без особой на то необходимости.
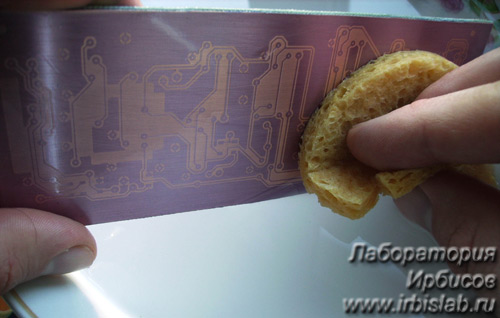
Рисунок 5 – Процесс проявки
Как только всё, что нужно, смоется, заготовку необходимо промокнуть х/б тканью и не промывая в чистой воде, дать просохнуть при комнатной температуре минимум полчаса, чтобы размягчённый содовым раствором фоторезист просох и затвердел. Если сразу начать травить, то возможно отслоение тонких дорожек. Хотя, возможно это происходит из-за того, что моему фоторезисту уже 2,5 года и его гарантийный срок хранения давно истёк.
Травление:
Обычно я сначала окунаю плату в раствор для травления секунд на 30, вынимаю, прополаскиваю в воде и смотрю: нет ли где несмытых участков фоторезиста или повреждений рисунка. В первом случае вам поможет иголка, во втором, если повреждения мелкие (обычно обходится без них) – лак для ногтей.
После травления фоторезист смывать пока не нужно, он ещё понадобится.
Важный момент: ещё на этапе проектирования платы все отверстия следует сделать диаметром (0,5-0,6) мм – это оптимальное значение, выявленное в результате проб и ошибок. Для чего это нужно: такое отверстие в меди и фоторезисте позволяет обойтись без накернивания, сверло само центруется. Сверлим отверстия.
В результате сверления, в местах выхода сверла образуются заусенцы, тут-то и помогает несмытый фоторезист! – зачищаем заусенцы мелкой шкуркой под струей воды, при этом прочная плёнка фоторезиста защищает дорожки. Как только кое-где начинает проступать медь – процесс шлифовки заусенцев можно считать оконченным (при изготовлении данной платы я забыл про этот этап, смыл фоторезист до сверления и пришлось потом немало повозиться.
Смывка фоторезиста:
Производитель рекомендует использовать каустическую соду или 10 % раствор нашатыря, но каустик, т.е. NaOH – едкий натр, опасное (сильнодействующая щёлочь) и сложно доставаемое вещество, нашатырь – как минимум неприятное, к тому же здорово окисляет медь, между тем фоторезист успешно смывается спиртом или ацетоном. Ацетон так же был забракован – эффективность намного ниже, чем у спирта и тоже окисляет медь. Спирт – вещество ценное
, потому здесь я для экономии применил пакетик с замком – в него кладется наша многострадальная заготовка, заливается всего несколько миллилитров спирта – лишь бы хватило на смачивание всей поверхности, всё это необходимо пальцами разгладить так, чтобы спирт смочил всю поверхность платы. Теперь можно сходить попить чаю – по возвращении весь фоторезист отпадёт и медь будет в отличном состоянии.
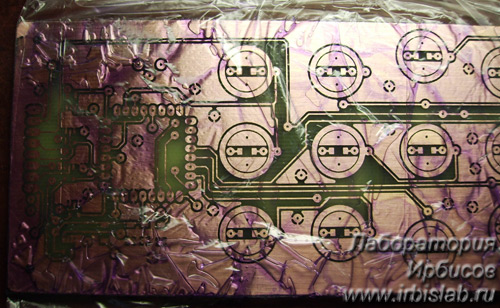
Рисунок 6 – Смывка фоторезиста
Совет: по окончании процесса необходимо вынуть плату из пакетика и как можно быстрее поместить под струю воды, тогда будут начисто смыты все остатки фоторезиста, если же дать спирту испариться (а делает он это весьма быстро) – потом замучаетесь отдирать – снова потребуется отмачивать в спирте.
Теперь не забудьте ещё раз осмотреть плату на предмет непротравленных участков и «прозвонить» на отсутствие коротких замыканий. Это является залогом надёжной работы устройства, к тому же потом уйдёт куда больше времени и сил, если какая-нибудь многовыводная микросхема выйдет из строя лишь потому, что кое-кто поленился досконально проверить плату.
Теперь осталось только нанести паяльную маску, в качестве шаблона для неё используется изображение на плёнке одних лишь выводов, без отверстий. Обычно это можно задать в опциях печати. Почти все программы для разработки печатных плат имеют возможность вывести на печать паяльную маску сразу, но тут имеется особенность – маска идет с отступом от краев контактных площадок, что при малом расстоянии между выводами может привести к отсутствию разделения их маской. Лучше просто напечатать одни выводы – так выходит куда более качественная маска.
Весь процесс повторяется – обезжиривание (только уже без шкурки, одним порошком), ламинирование, засветка каждой стороны – причём уже не надо делать бутерброд – достаточно наложить фотошаблон маски и прижать стеклом. Снова проявка, сушка и получается вот это:

Рисунок 7 – Готовая к лужению плата
Всё! Можно лудить. Подсушенный фоторезист стоек к температуре паяльника, хотя я и использую припои с низкой температурой плавления (145 °С). Так же следует применять жидкие флюсы без канифоли, которая оставляет практически несмываемые следы, к тому же маска боится спирта. Я применял флюс «Для пайки алюминия». Алюминий он, конечно же, не позволяет залудить, зато медь – на ура, не портит вид платы и легко смывается водой всё с тем же стиральным порошком.
Теперь можно приступать к монтажу вашего устройства!